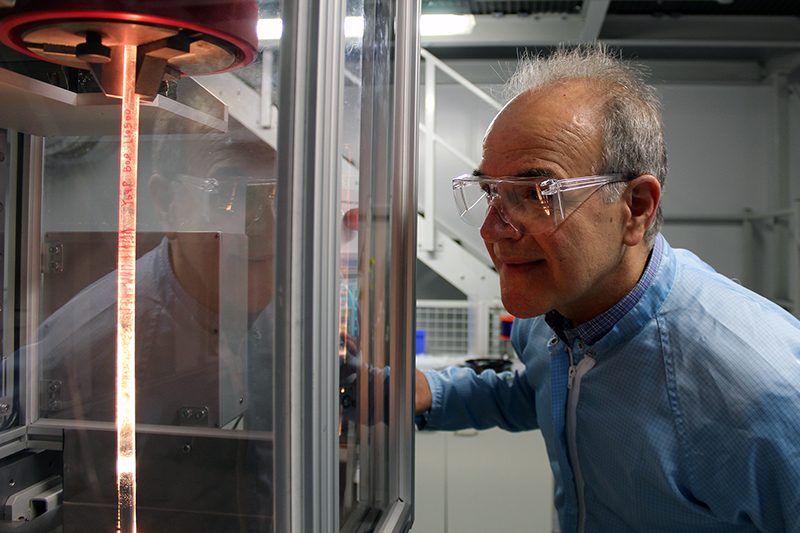
How fibre lasers can help save the planet
High power fibre laser technology boasts many unique features that set it apart from other competing technologies and could be the key to making manufacturing more efficient and sustainable. High power fibre lasers are now routinely produced around the world and widely used in the most advanced production lines for cutting, welding and 3D printing. Professor Michalis Zervas, a Co-Investigator in the Future Photonics Hub, shares his expertise on the environmental benefits of fibre laser technology and its potential as the industry enters the digital manufacturing era.
How can laser technology contribute to sustainable manufacturing?
Laser technology is at the heart of modern manufacturing. High power fibre laser technology is the latest entry into the manufacturing arena and it has features that set it apart. Unlike competing solid-state and other laser technologies, fibre lasers have the smallest footprint and fast turn-on key operations due to their monolithic, all-fibre, compact cavities. They have unprecedented stability, power scalability and world record efficiency – the overall efficiency of turning electrons into light. Fibre laser technology has the potential to revolutionise the industry and be used like never before.
How much power could fibre lasers save?
Power efficiency is one of the most important aspects of fibre laser technology. They show wall plug efficiency – the energy conversion efficiency with which the system converts electrical power into optical power – of more than 40 per cent when competing technologies are 10 per cent and less. That makes a huge impact on electricity savings and process efficiency and only fibre laser technology can deliver these savings.
I am involved with a company called SPI Lasers, which has produced advanced fibre laser technologies for digital manufacturing. Our conservative calculations show that these new fibres lasers could result in roughly 250 thousand tons of CO2 reduction per year, just by reducing the electricity that is needed to run the lasers. That does not include the savings acquired because you have a much more efficient process. Routinely, the latest generation of fibre lasers can even half the energy requirements for a large number of material processing applications.
These savings are extremely timely – the UK needs to deliver on its net zero carbon objectives. More research and investment are needed to develop the next generation of agile fibre laser manufacturing tools to reap the sustainable rewards of fibre lasers’ unique attributes.
What is it about fibre laser technology that has such a positive, sustainable impact?
It is all about the unique and highly efficient ways of structuring light offered by the fibre technology. The special techniques we use to shape the light (both the beam shapes and polarisation) are done in an innovative way at multi-kilowatt levels so they double the efficiency of the process. This is a result of the excellent beam control and uninterrupted light guiding properties, seamless connections and efficient heat removal offered by fibres. You are able to shape the beam to specific manufacturing requirements. So, even if you have the same power, because it’s shaped properly, the efficiency can be doubled. Only fibre lasers can deliver this efficiency.
What extended benefits are there from using this technology?
By having a more efficient process you can go faster. By shaping the beam to fit the process, we have shown a 30 per cent faster processing speed and you’re doing that with half the power that traditional laser technology requires. Additionally, fibre laser technology allows you to have smaller processing units, so they become more flexible, efficient, versatile and easy to integrate into more complex manufacturing systems.
Which other sectors can benefit from this type of technology?
Manufacturing is at the centre of our economy and effects all modern life. Its skills and properties feed into other sectors and industries all the time – the great majority of cars are now welded with processes using lasers for example. Aerospace industry is also benefiting from fibre laser technology manufacturing and the health and medical sector are now using these super stable lasers. For example, stent cutting has been revolutionised and is now being done entirely with fibre lasers because of the stability and precision of these lasers. The manufacturing of bespoke prosthetics has also changed significantly through the introduction of fibre lasers in additive manufacturing, again, for the same reasons of stability and precision. We are now starting to even think about novel powerful fibre lasers with mega-Watt output powers. These could be used for particle acceleration in table-top mini CERNs, cleaning-up the space debris, or even treating nuclear waste, in order to make the world a better, cleaner, more prosperous and safer place.
How do programmes like the Hub support the development of fibre laser technology?
The Hub is absolutely critical in taking the ideas we have and the basic technology that we develop into industry. Industry is excited by ideas, but they want ideas which are proven and practical. Never underestimate the amount of work, effort, time and innovation that is needed to transfer a concept or idea from the lab and turn it into a practical solution. Some of the most important breakthroughs, patents and IP are generated at that stage where you transfer the basic idea into a manufacturable and deployable solution. This is where the Hub is essential. Taking an idea into the real world takes another set of skills and attitude and this is exactly what the Hub cultivates and provides. The Hub bridges the gap between the academic environment and industry.
What does the future hold for fibre laser technology and sustainable manufacturing?
It’s widely recognised that this area will see unprecedented growth and expansion over the next five to ten years and displace existing technologies to even larger extent. By the end of this decade, fibre lasers are projected to be to a $10 billion business. But despite the success and growth we’ve already seen, high power fibre lasers are still in their infancy and we’ve only just scratched the surface of this technology. We are still using fibre lasers in a primitive way as single-channel, single colour, unpolarised, unshaped, raw power providers. We know that the lasers can guide and shape light but you can also control the polarisation of light and control the wavelength of light and you can deliver this over long distances. At the moment we are barely using these unique attributes. These are the properties that will start to be used going forward and will create the digital factories of the future with flexible workfloors that are bespoke to the application. We believe this is a new paradigm of how lasers or photons can be generated and delivered and will have a tremendous impact on shaping the upcoming digital manufacturing era.